Enterprise Asset Management users can gain extra benefits from optimizing inventories of replacement units, spare parts, and consumables.
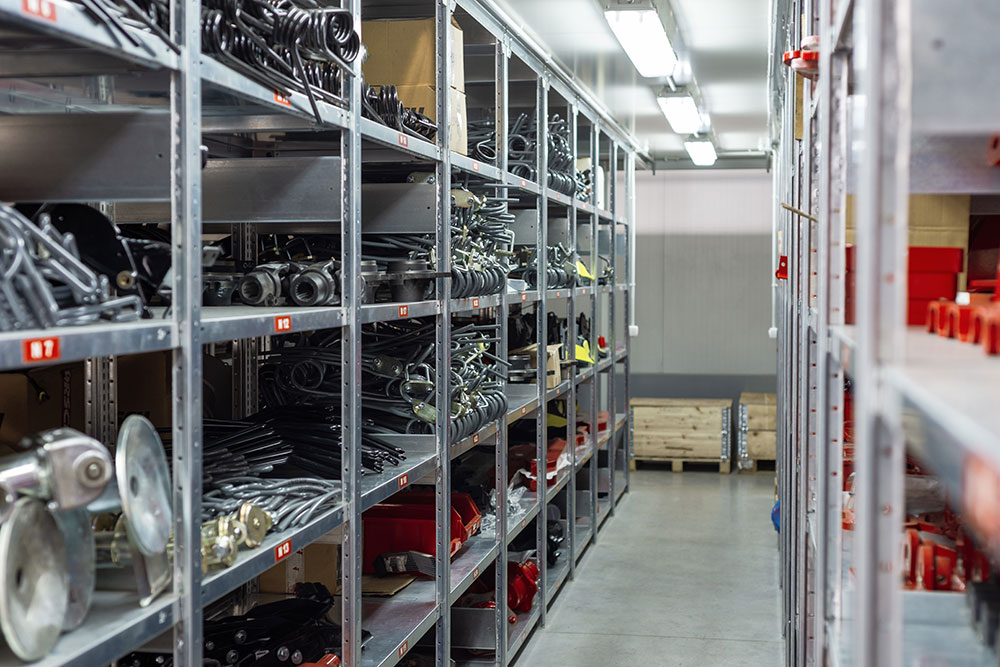
The use of asset enterprise management to manage inventory ensures the availability of the right parts in the correct location.
October 8, 2019
By Nathan Eichelberger, Vice President, Accruent
Most organizations invest in and use their Enterprise Asset Management (EAM) systems primarily to manage maintenance work orders for their big-ticket items like conveyors, robots, CNC machines, pumps, and extruders. Sure, those are important and justify setting up EAM in the first place. But, too many EAM users are missing out on the significant benefits possible from using their system to manage and optimize inventories of replacement units, spare parts, and consumable supplies.
Especially for organizations that are spread across multiple locations, an EAM can save tens of thousands, or even hundreds of thousands of dollars in annual operating expenses, not to mention working capital. And, there’s also the opportunity to reduce or totally avoid inventory stock-outs, which can result in unplanned plant shutdowns or expensive emergency re-supply orders.
There are several clear benefits from using EAM to manage inventory, as well as a handful of steps that typically lead to success.
BENEFITS
- Availability of the right parts. Having the necessary parts on hand when they are needed is critical to having efficient maintenance processes and avoiding prolonged costly unplanned downtime. While inventory management may seem straightforward, many factors add to its complexity. For example, the lead time to get certain parts, as well as the rate at which parts are used, both affect the number of items a company should keep in stock.
- Locate parts faster. In many organizations, quickly locating parts can be a challenge. Barcode scanning and inventory tracking capabilities within an EAM can make finding parts much easier, translating to faster repair times and more efficient labor.
- Control costs. An EAM can provide valuable insight into parts utilization and costing. It becomes easier to see an actual spend on individual parts and improves part sourcing to reduce inventory costs.
- Avoid stock-outs. Many EAMs also offer capabilities for automated inventory control that streamline the inventory process. Using features like min/max values and predefined reorder points can help avoid downtime-extending stockouts.
- Capitalize on your scale. Larger organizations have the option for their EAM to manage inventory on an enterprise-wide basis. When two sites are physically close to one another and have similar equipment, an EAM can reduce inventory by sharing stock across sites.
- Realize more ROI from your EAM. Why base your entire EAM business case on maintenance work order improvements? If you’re still in the consideration phase of adding an EAM system, build inventory cost savings into the benefit side of the ledger. If your EAM is already in place, generate support for your next plant maintenance investment by showing the CFO how you’re freeing up funds through your EAM inventory program.
STEPS FOR SUCCESS
- Ensure your system has the capability. The first step is to validate that your current (or planned) EAM system has the ability to track, manage, and optimize replacement units, spare parts, and consumable supplies. While it’s a common feature in full-functionality EAM systems, how the system is implemented can be a major determinant in whether you’ll achieve maximum benefits.
- Assign an advocate. A barrier to many organizations in benefiting from the inventory optimization capabilities of an EAM is that there’s no one single person tasked with generating success in this area. You can start by giving that assignment to a specific plant engineer, operations manager, or production planner. Give them a specific assignment, add it to their written job responsibilities, and provide recognition or incentives for defining a program and quantifying success.
- Benchmark. One sure-fire means to start realizing inventory management benefits from an EAM is to measure how you’re doing now, and over time. After all, what’s measured is what gets paid attention to. You might also get industry-specific parts inventory data from your industry association or from your EAM vendor.
- Consider phasing in parts. While it might seem overwhelming to incorporate all the data about all your replacement units, spare parts, and consumable supplies, you can start seeing the benefits by starting small. Consider beginning with the parts associated with the primary systems used throughout your different plants. Once you see the process and benefits from that one set of components, it will become easier to add subsequent spare parts for additional systems.
- Standardize your nomenclature. One of the challenges, and opportunities, of EAM systems is that different plants and people might be applying different names and titles to the same parts. I have seen numerous examples of data issues, which I’ll illustrate through the example of a Daifuku Wynright conveyor. A manufacturing plant may have a parts database that includes these conveyors listed under Daifuku in some instances and Wynright in others. The model name may be entered four different ways and the associated classification code may be represented 10 different ways. In this simple example, which outlines a common struggle for many parts databases, there can be 80 different permutations for representing the same conveyor.
- Get help from an expert or peers. If you’re still unsure how to proceed, there are two paths to take for advice. The first is by tapping into forums or networks among your industry association. The second is by going straight to your EAM vendor and asking for their help.
- Promote success. Finally, the way to get the most out of this hidden gem in your EAM is to tell people across your company about the success you’re having. After all, success breeds success. If you take the phased-in approach, and have set benchmarks, after you start to see the needle move it’s time to share that good news with people who can make progress with other spare parts and components in other systems in other plants. It can work!
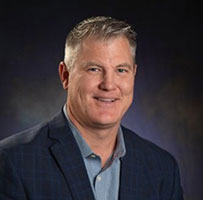
Nathan Eichelberger
Nathan Eichelberger is a Senior Vice President responsible for Accruent’s client relationships across multiple industry sectors, including discrete and process manufacturing, distribution and utilities. He has 24 years of experience in technology leadership, and built his career developing collaborative relationships to achieve innovative solutions for his teams and customers. Prior to joining Accruent, his career encompassed executive roles at Gateway Computers, LANDESK Software, and Ivanti Software.
Accruent